Benefits
Comparative Chart Coconut Fiber Acoustic
Insulation Material
|
Sound Absorption
|
Effective Frequency Range
|
Notable Acoustic Features
|
---|---|---|---|
Coconut Fiber (Coir)
|
0.75–0.97
|
250 Hz–4000 Hz
|
Excellent absorption at mid to high frequencies; competitive with synthetics; especially effective when used with perforated panels or porous backings
|
Sheep Wool
|
0.60–0.90
|
250 Hz–4000 Hz
|
Strong broadband performance; humidity resilient; natural sound regulator.
|
Cotton Fiber (Denim)
|
0.70–0.90
|
500 Hz–4000 Hz
|
High absorption at mid–high frequencies; non-toxic
|
Hemp Fiber
|
0.60–0.85
|
500 Hz–3150 Hz
|
Absorbs well in speech frequency range; naturally resistant to mold.
|
Cellulose Fiber
|
0.65–0.85
|
500 Hz–4000 Hz
|
Suitable across a range of frequencies; high recycled content; often used as blown insulation.
|
Straw
|
0.50 - 0.70
|
500 Hz–2000 Hz
|
Moderate performance; best in thicker bales; less dense than coir.
|
Comparative Chart Fiber Thermal Conductivity
Insulation Material
|
Thermal Conductivity (W/m·K)
|
Typical R-Value
|
Notable Properties
|
---|---|---|---|
Coconut Fiber (Coir)
|
0.041 – 0.048
|
~2.0–2.4 (1" thick)
|
Good moisture resistance, eco-friendly, renewable
|
Sheep Wool
|
0.035 – 0.040
|
~3.7 (1" thick)
|
Regulates humidity, naturally fire retardant
|
Cotton (Denim)
|
0.037–0.040
|
~3.8 (1" thick)
|
Recycled content, non-toxic
|
Hemp
|
0.040 – 0.045
|
~3.5 (1" thick)
|
Mold-resistant, good breathability
|
Cellulose
|
0.039 – 0.045
|
~3.2–3.8 (1" thick)
|
High recycled content, effective air barrier
|
Straw bale
|
0.045 – 0.065
|
~2.0–2.7 (1" thick)
|
Thick, load-bearing, renewable
|
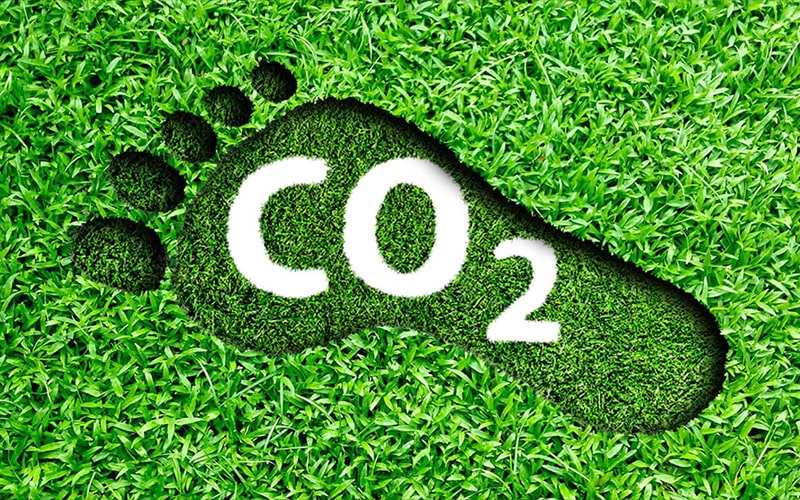
Key Benefits of EVA Coir Fiber Insulation
Natural performance meets cutting-edge engineering. Discover why EVA Insulation is the smarter, safer choice for sustainable building.
01 Higher R-Value
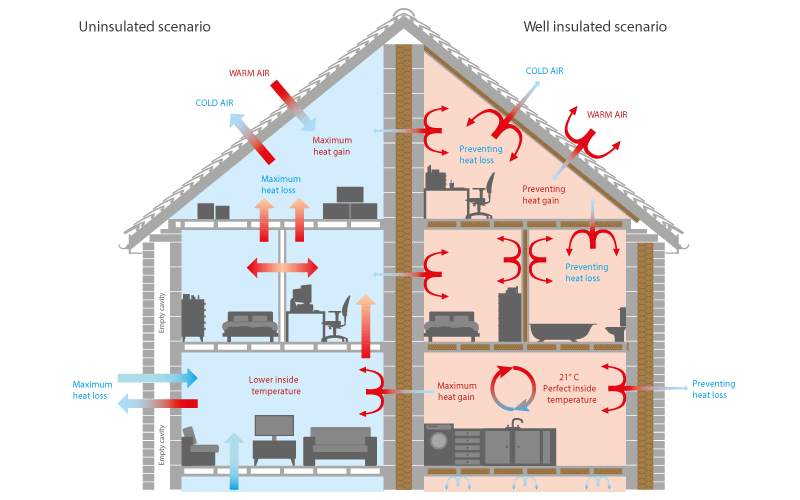
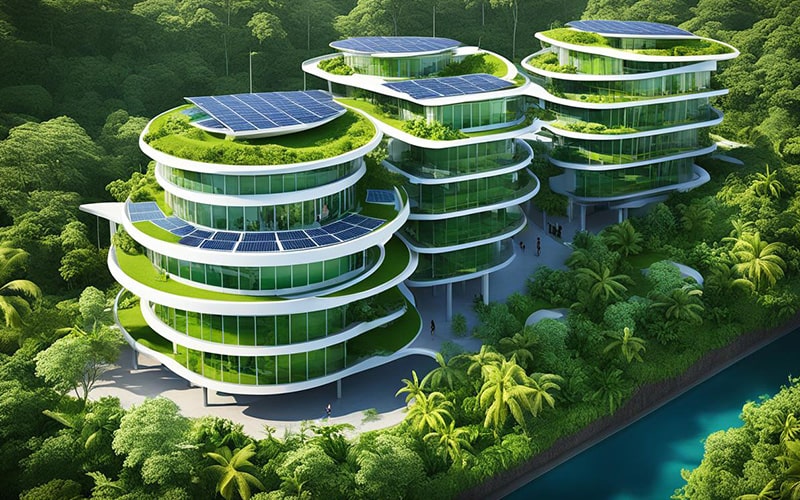
02 Energy Efficient Living
03 Comfort That Lasts
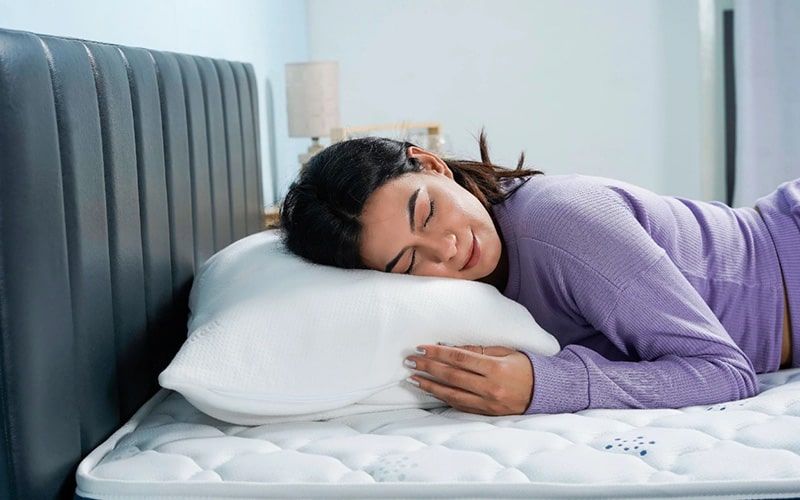
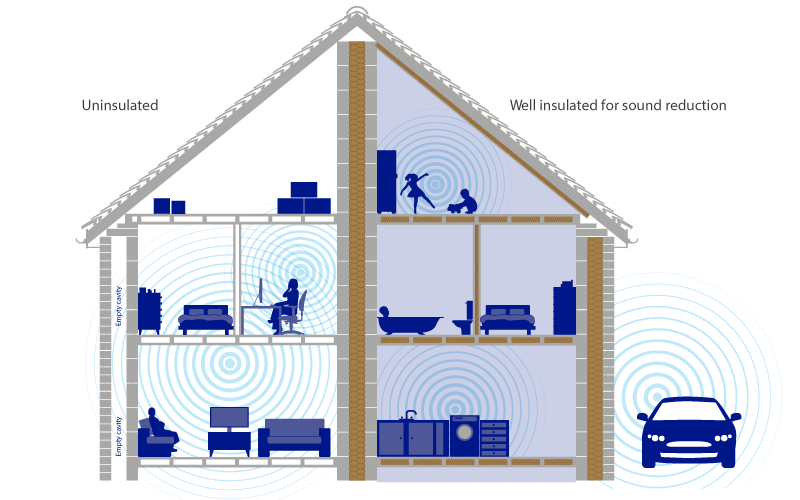
04 Built-In Noise Control
05 Fire-Safe by Design
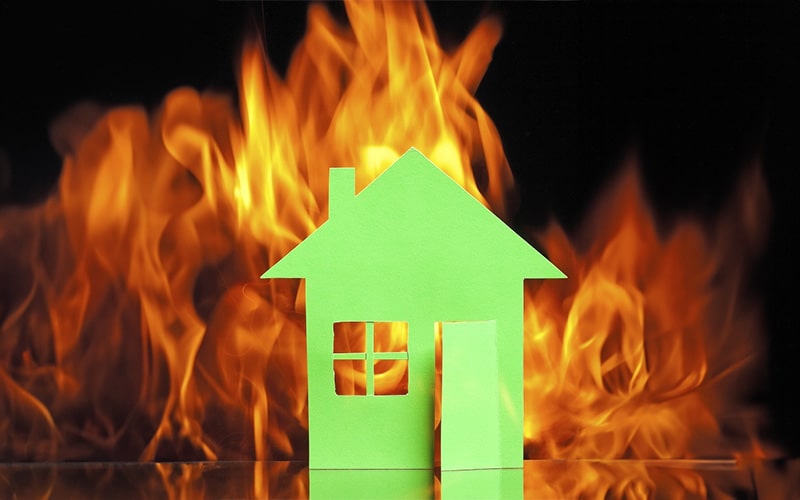
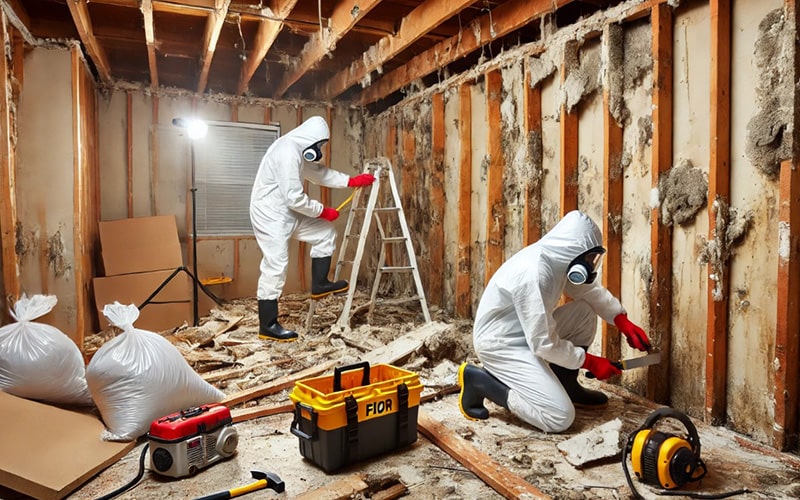
06 Moisture & Mold Protection
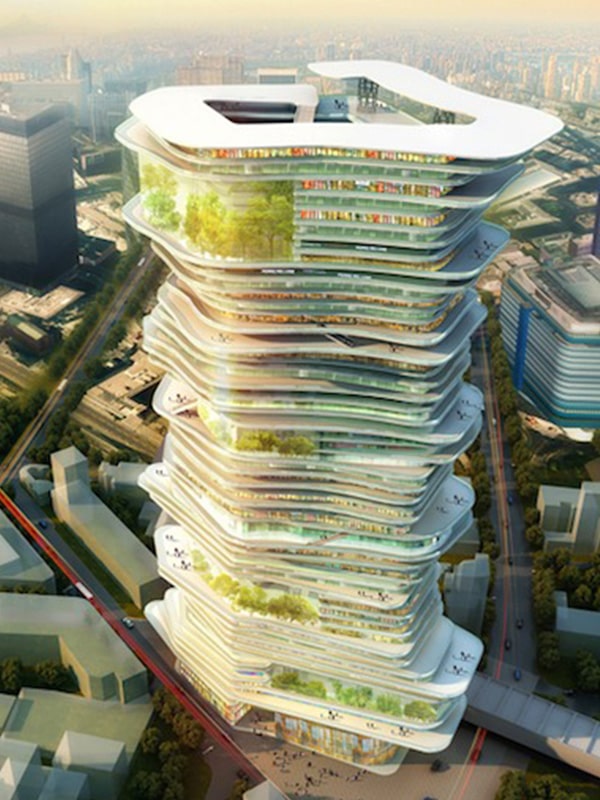
Applications in Modern Construction
- Wall Insulation
- Roof Insulation
- Ceiling and Wall Panels
- Eco-Friendly Building Materials
- Sound Insulation
- Composite Materials
- Flooring Solutions
- Sustainable Construction Practices
Why It Matters
Every EVA panel is built with purpose providing thermal and acoustic insulation that’s smart, safe, and truly sustainable. From sourcing to shipping, we ensure comfort doesn’t cost the planet.
Production
What is Coconut Fiber?
Coconut fiber, or coir fiber, is a natural material extracted from the husk of mature coconuts. Known for its strength, durability, and eco-friendly properties, it’s used in a wide range of industries including textiles, insulation, mats, ropes, and horticulture. Its production combines time-tested techniques and modern advancements to create a sustainable material suited for today’s eco-conscious world.

Our Manufacturing Process
Harvesting & Dehusking
Mature coconuts are harvested and dehusked to separate the fibrous shell, which makes up 35% of the coconut’s weight and contains durable, high-quality fibers for further processing.
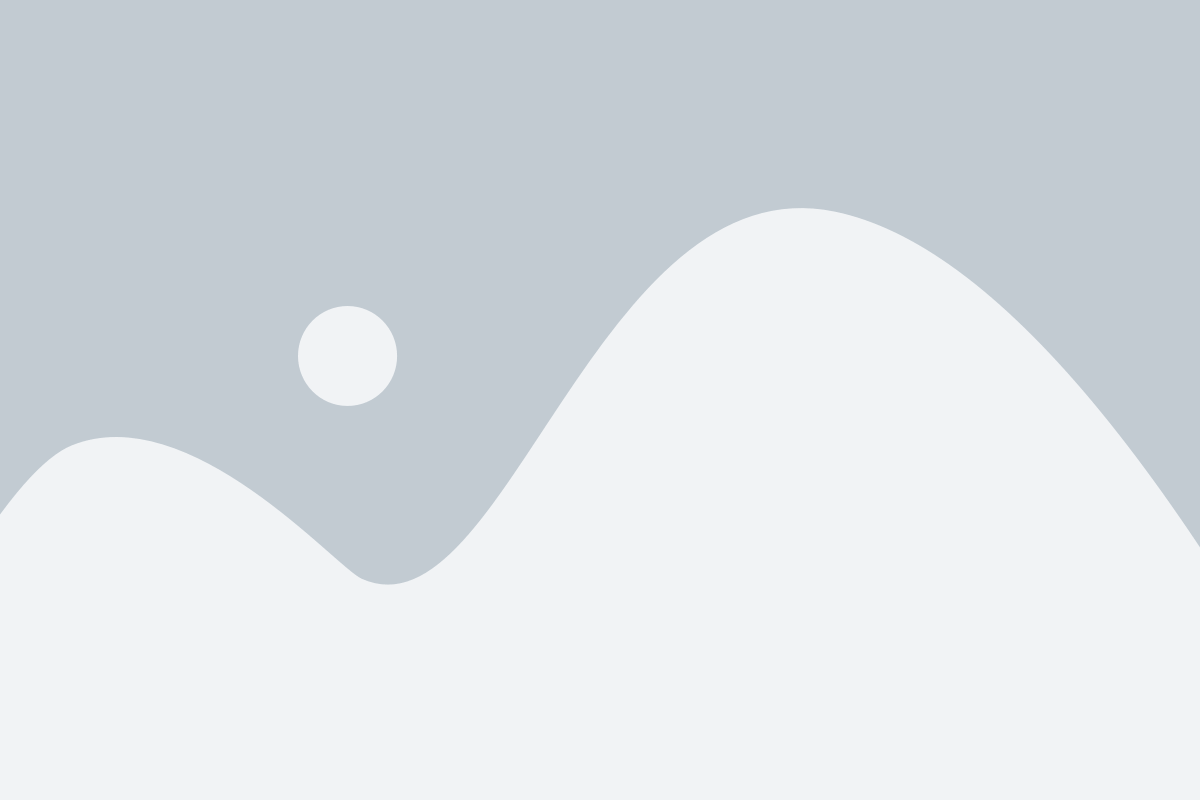
Soaking & Retting
Husks are soaked to loosen fibers, using traditional fermentation or modern enzyme-based methods that reduce retting time, enhance fiber quality, and support environmentally sustainable processing.
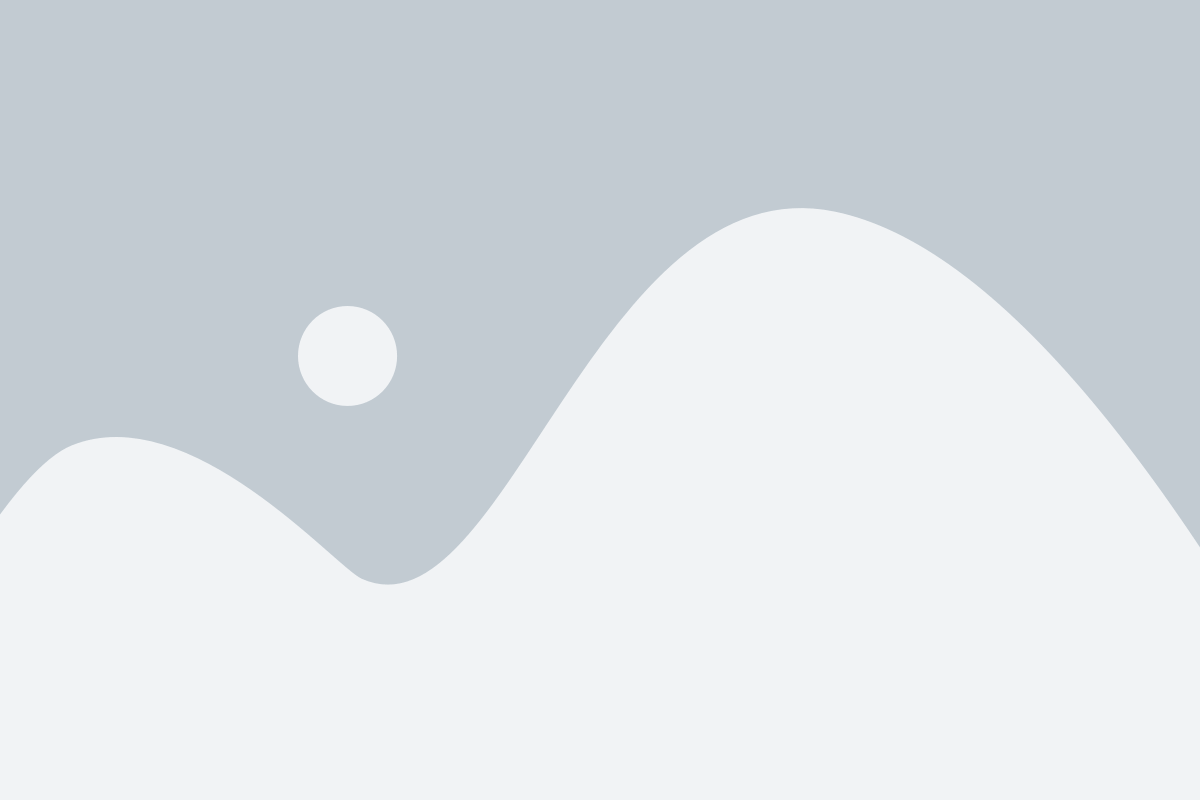
Fiber Extraction Techniques
Retted husks are processed through traditional, mechanical, or green decortication to extract fibers efficiently, ensuring optimal quality for various industrial and eco-friendly applications.
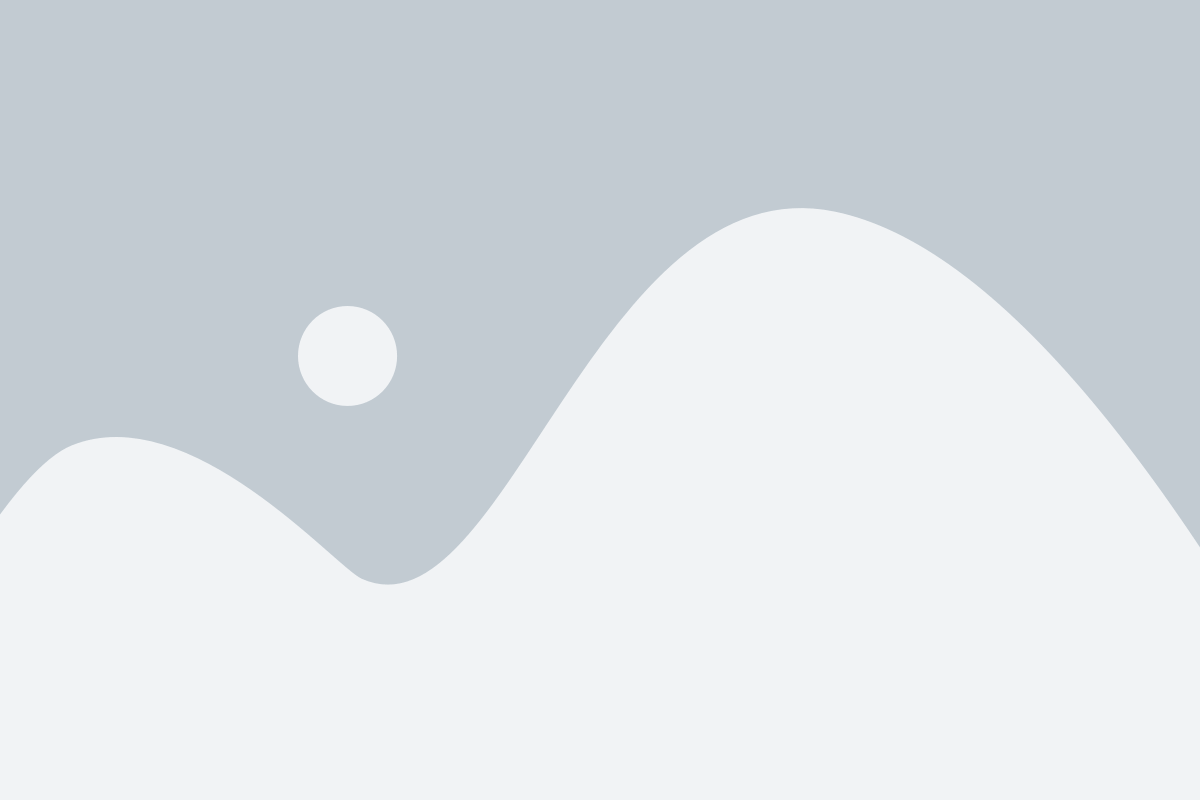
Cleaning & Drying
Extracted fibers are thoroughly cleaned to remove impurities, then dried naturally or mechanically to achieve ideal moisture levels, ensuring quality, longevity, and readiness for processing or export.
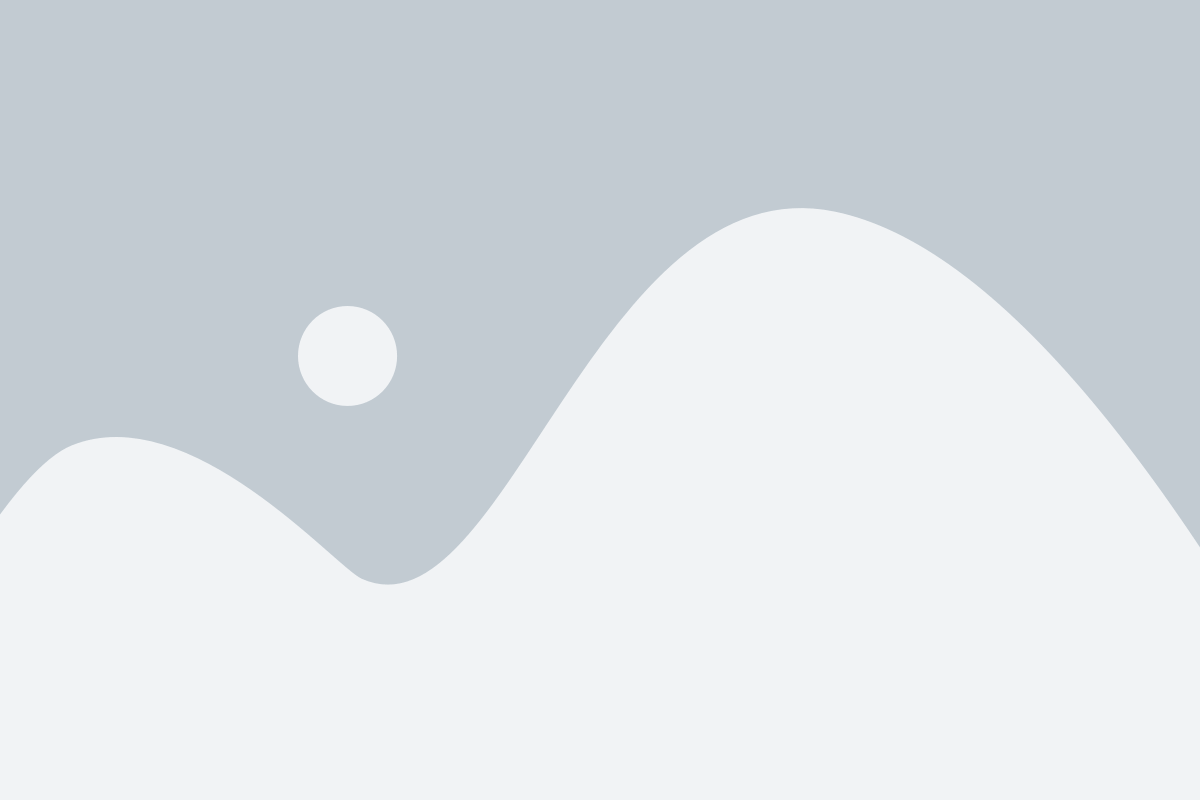
Final Processing
Cleaned fibers are converted into yarn, mats, or blocks tailored for specific applications like horticulture and insulation, ensuring performance, usability, and efficient logistics.
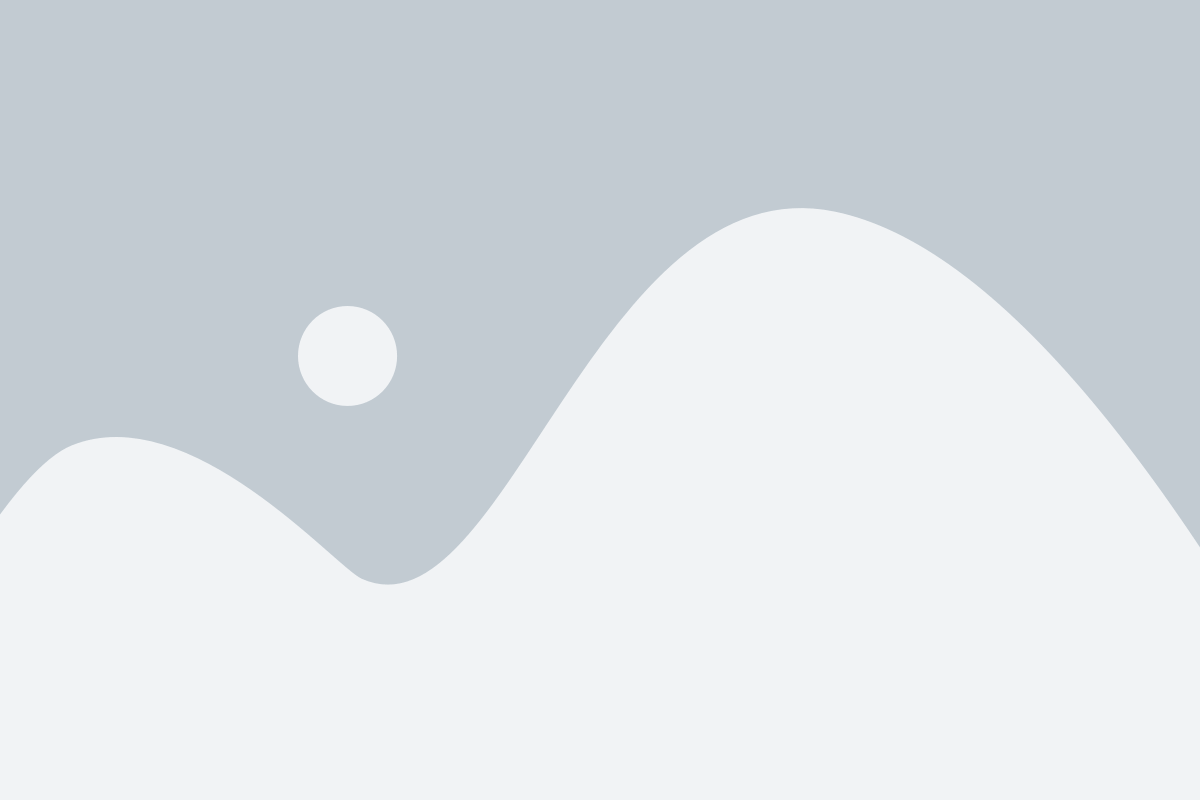
Baling and Packaging
Processed fibers are baled and packaged using eco-friendly materials, ensuring protection, easy transport, and traceability, while maintaining quality throughout storage and distribution.
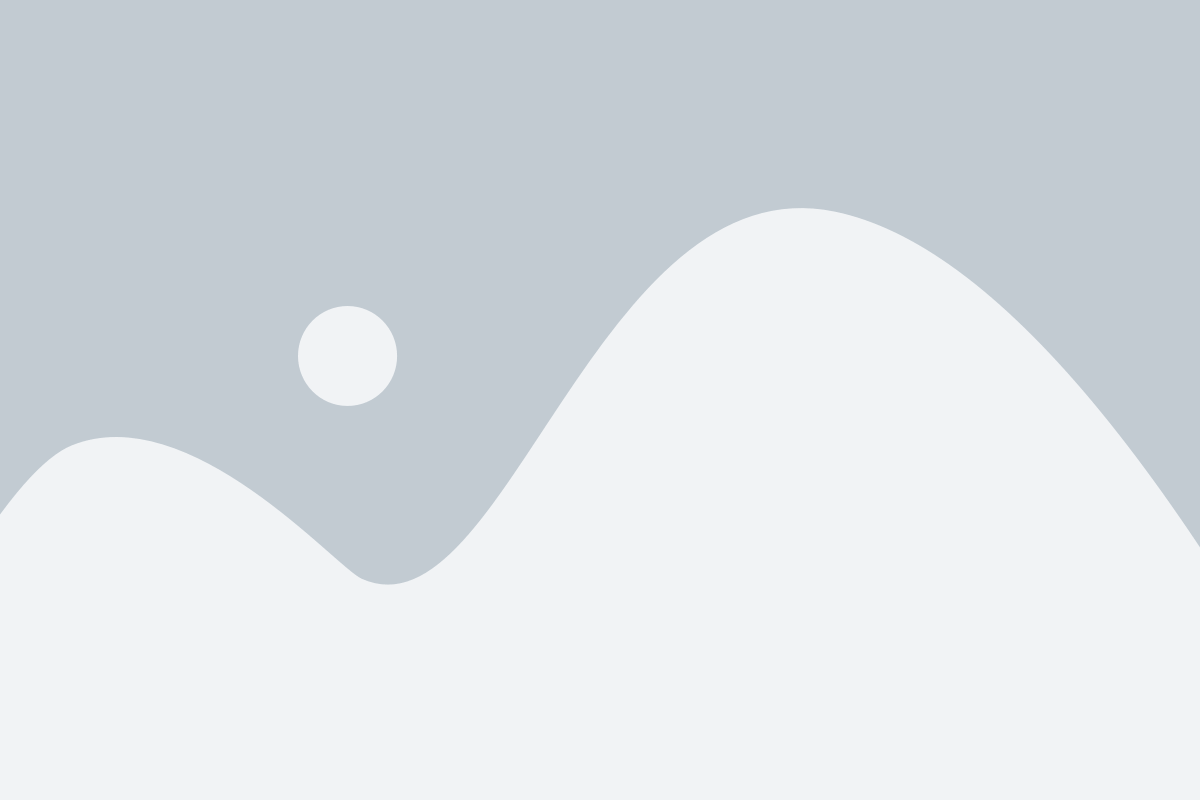
Quality Control at Every Stage
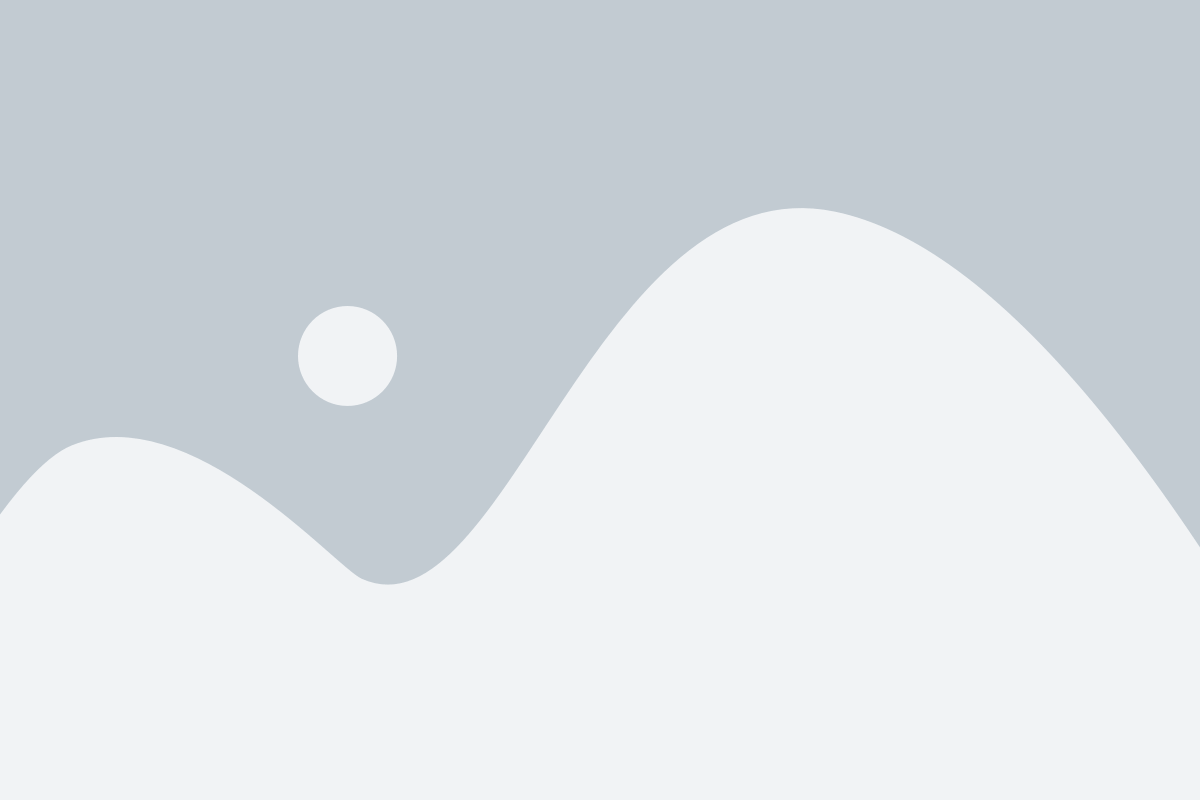
Moisture Content Testing
We test fiber moisture levels to stay within 20–25%, preventing bacteria and fungi growth during storage and transportation, ensuring product stability and quality.
pH Level Testing
The pH of coconut fiber is maintained neutral to slightly alkaline, crucial for plant compatibility in horticultural applications, ensuring optimal soil health and performance in growing environments.
Electrical Conductivity (EC) Testing
EC testing measures salt content and nutrient levels, ensuring fibers fall within safe thresholds for plant roots, using wet and dry methods to guarantee safe, grow-ready materials.
Purity Checks
We ensure every fiber batch is free from impurities like sand, stones, or debris, enhancing performance in applications like insulation or potting mediums by maintaining consistency &purity.
Regular Inspections
Rigorous inspections are conducted throughout production—from raw materials to packaging—ensuring each batch meets internal benchmarks and global standards, delivering the highest quality coconut fiber products.
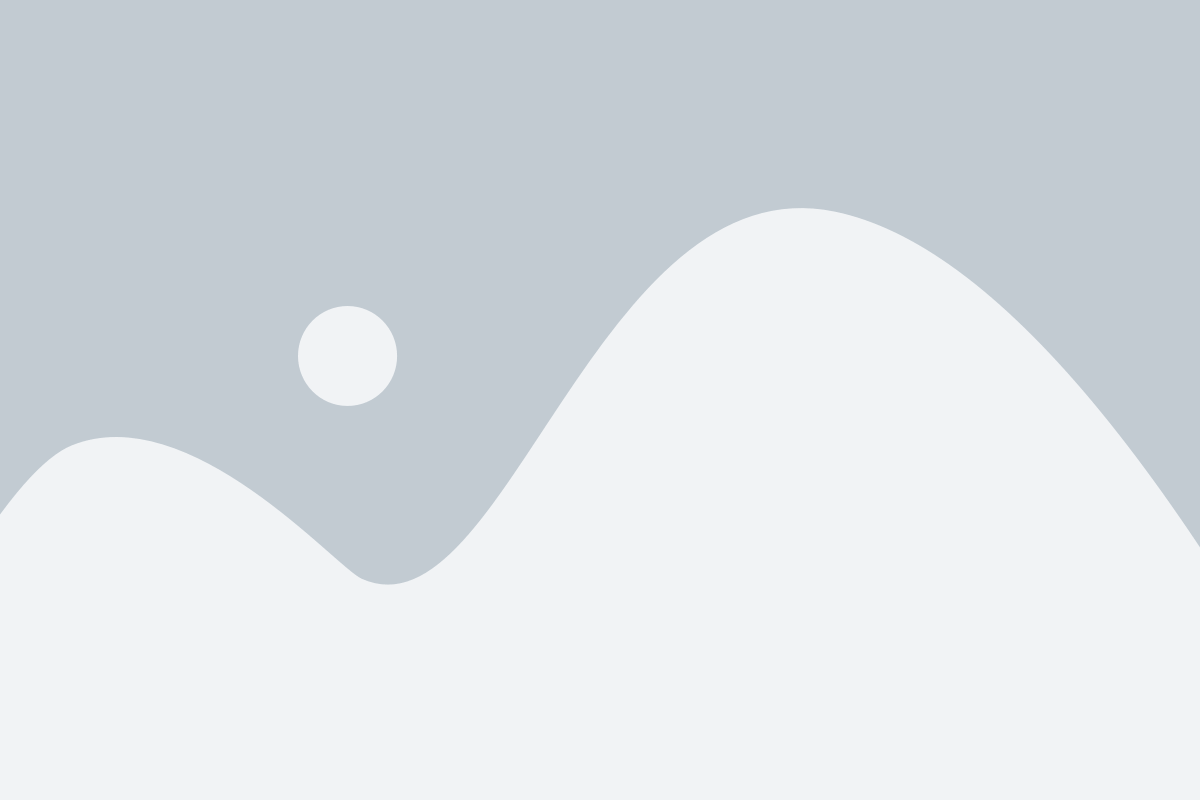
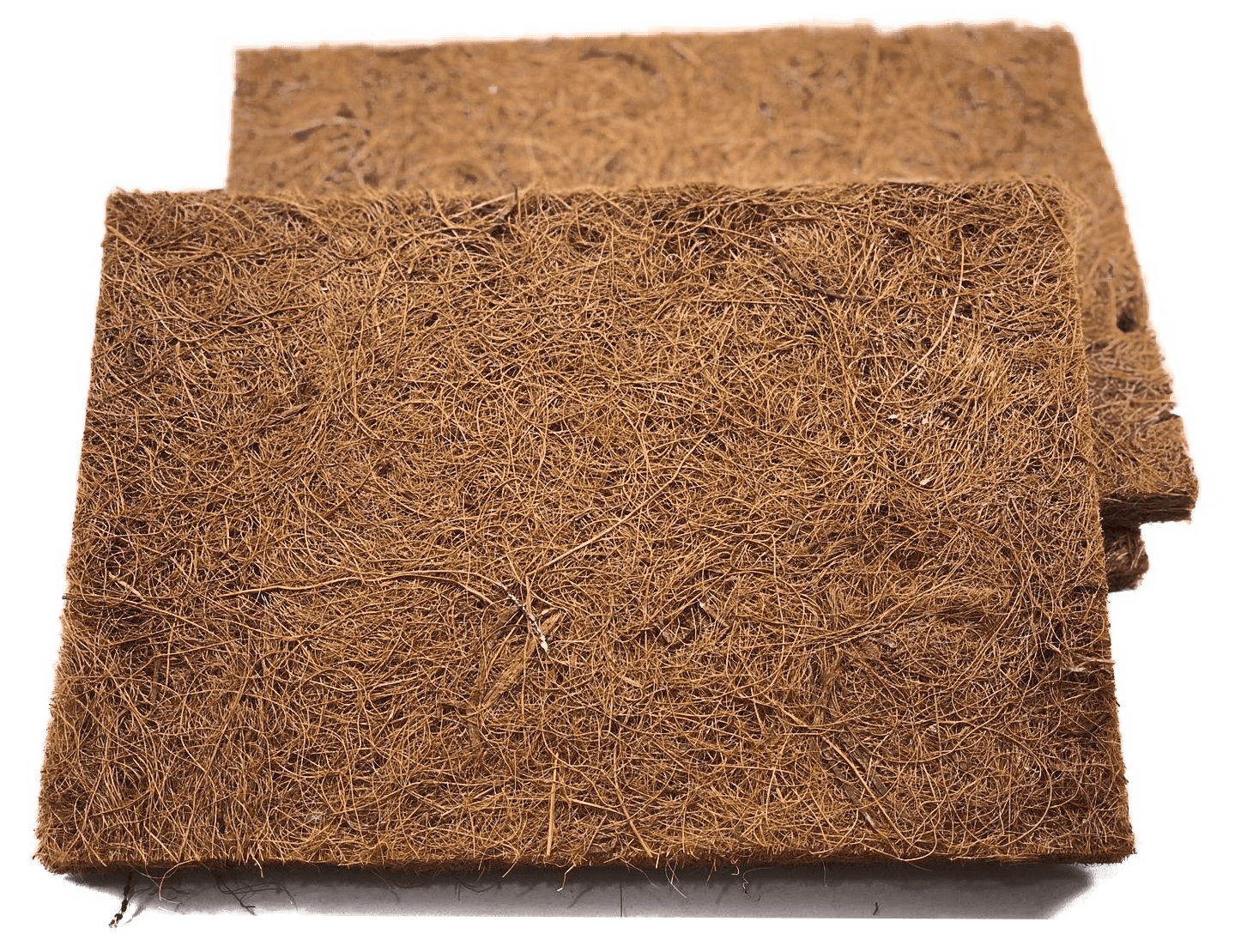
Blending Tradition with Innovation
At Eva Insulation, we bring together generations of traditional expertise and cutting-edge engineering to create high-performance insulation solutions from natural coconut fiber. Our deep-rooted understanding of the material, combined with advanced manufacturing practices, allows us to produce eco-friendly products that meet the evolving demands of modern industries.
We prioritize both sustainability and innovation, ensuring that every fiber we process supports environmental well-being while delivering superior thermal and acoustic performance. By adhering to international standards and continuously refining our processes, Eva Insulation stands as a global benchmark in coconut fiber manufacturing—trusted by industries seeking reliability, efficiency, and a greener future.